Modifizierung von styrolbasierten TPE mit Kurzfasern
Projektleiter: Dr. Axel Nechwatal
Projektnummer: BMWi / IGF - 20837 BG
Laufzeit: 01.10.2019 bis 30.09.2021
Aufgabenstellung
Ziel dieses Projektes war, styrolbasierte thermoplastische Elastomere (TPS) zu entwickeln, die sich von vergleichbaren Materialien durch eine höhere thermische Formbeständigkeit abheben. Basierend auf früheren Arbeiten an Gummiwerkstoffen bestand der Ansatz dazu in der Modifizierung der TPS mit kurzen, nicht-starren Fasern. Diese Untersuchungen liefen als Gemeinschaftsprojekt mit dem SKZ Würzburg.
Ergebnisse
Die zusammen mit dem SKZ Würzburg erarbeiten Ergebnisse an einer ganzen Bandbreite von TPS-Typen zeigten, dass mit einigen der ausgewählten Kurzschnitte eine direkte Compoundierung in das Elastomerblend möglich ist, während andere Fasern hier Schwierigkeiten bereiten. Eine homogene Faserverteilung erhält man mit Fasergranulaten. Mit steigender Faserkonzentration nehmen die Spannung bei niedriger Dehnung und die Härte der so modifizierten Compounds zu, die Zugfestigkeit und die Dehnung bei Zugfestigkeit ab. Die (verwendeten) Fasern unterscheiden sich qualitativ in ihrem Effekt, in jedem Fall wächst die Verstärkung aber mit steigender Länge. Die fasergefüllten TPS behalten ihre dynamische Beständigkeit; erst wenn man Menge und/oder Länge der Fasern über ein bestimmtes Maß erhöht, muss man mit Abstrichen rechnen. Bei höherer Temperatur fällt zwar die Steifheit des TPS auch bei Faserverstärkung ab, das Niveau verbleibt dennoch deutlich über dem Niveau des reinen Elastomers. Der Druckverformungsrest hängt mit der Ausrichtung der Fasern zusammen: Belastet man in Faserrichtung, quasi „auf die Fasern“, so findet man ein deutlich niedrigeres Niveau, senkrecht zur Faserrichtung dagegen erhöhte Werte.
Anwendung
TPE bilden innerhalb der Elastomere eine innovative Gruppe mit starken jährlichen Wachstumsraten. Der entscheidende technologische Vorteil von TPE gegenüber Gummi besteht darin, dass TPE zwar gummielastische Eigenschaften haben, aber nicht (irreversibel) vulkanisiert werden müssen. TPE lassen sich – genau wie andere Thermoplaste – immer wieder thermisch umformen. Entsprechend liegt die Produktivität deutlich höher als bei adäquaten Gummiprodukten. Die Nachteile der TPE ergeben sich aus ihrem größten Vorteil, nämlich ihrer thermoplastischen Natur: TPE-Produkte sind thermisch und auch dynamisch weniger belastbar als „normale“ Gummierzeugnisse. Vor allem aber weisen sie eine relativ hohe bleibende Verformung unter Druck auf.
Mit der hier gefundenen Lösung, ca. 2 % PES-Faser durch Doppelschneckencompoundierung in die Matrix einzubringen und somit einen höher wärmebeständigen Werkstoff bei gleicher Dichte und Härte darzustellen, wird es möglich, sowohl bereits bestehende TPE-Produktgruppen aufzuwerten als auch weiter in Marktsegmente vorzudringen, die bisher herkömmlichem Gummi oder anderen Kunststoffen vorbehalten waren.
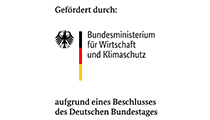
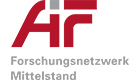
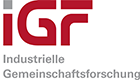